"Игры и Игрушки" №4-2013
Деревянная симфония
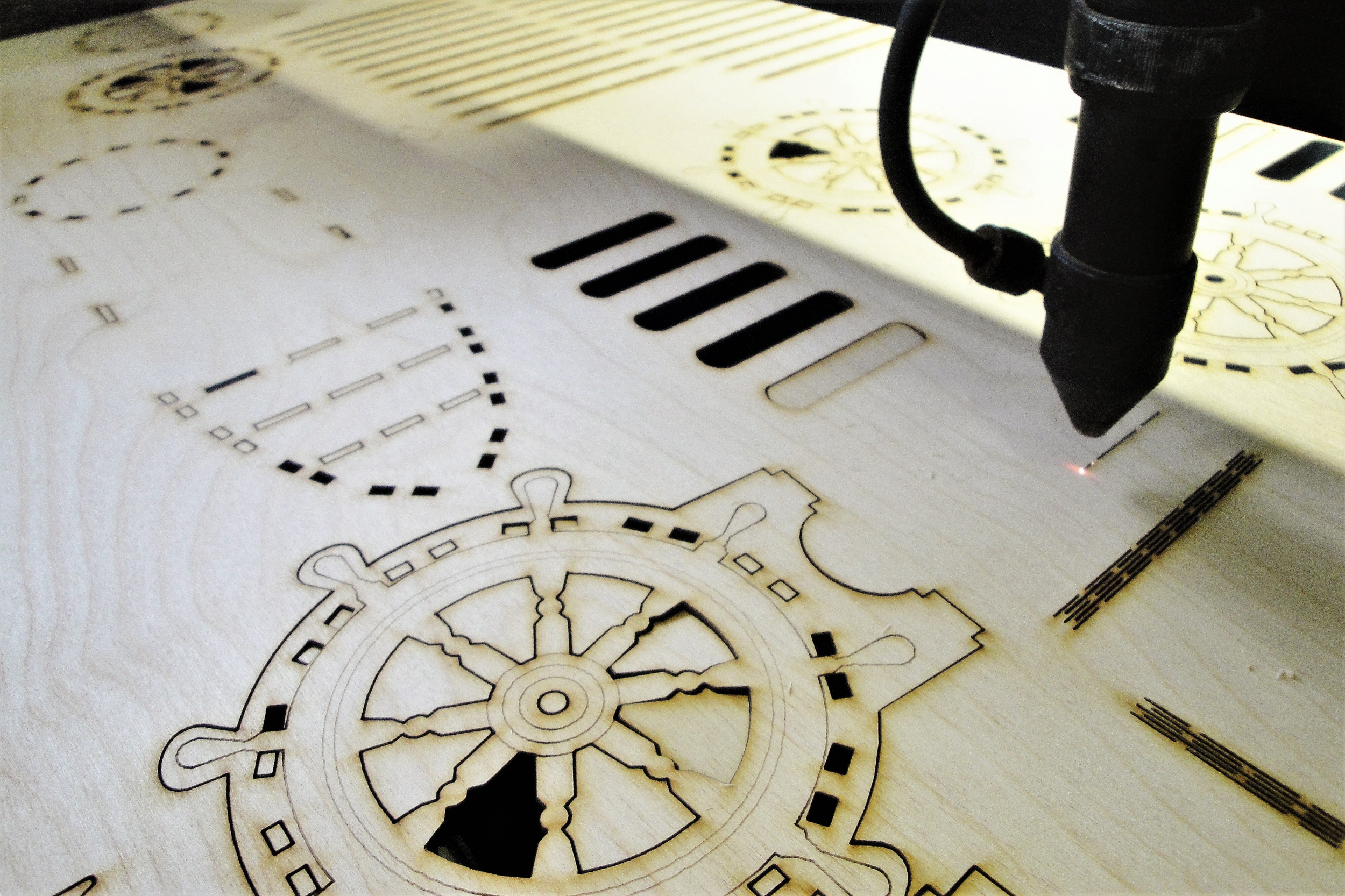
Мы смотрим на жизнь новаторски. Наше правило — из дерева можно сделать всё! И притом недорого.
Как нам это удаётся? Всё просто, мы опираемся на три одновременно работающие основы: новые технологии производства, креативное конструирование и сбалансированная экономика предприятия. Давайте узнаем, как создаются деревянные наборы для творчества. Причём не только для детей, но и для взрослых.
С чего начинается театр? — С вешалки. А производство? — С закупки материала.
Наши наборы мы изготавливаем из высших сортов шлифованной берёзовой фанеры марки ФК (на основе природного клея). Есть разные методы фигурной резки фанеры: фрезерование и лазерная резка. Наше предприятие предпочитает лазерную резку фанеры на станках с числовым программным управлением. Лазерный станок — это большой «принтер» с лазерной трубкой, подключённый к компьютеру и исполняющий чертёж из специализированной программы.
В нашей компании успешно преодолеваются ошибочные стереотипы восприятия дерева как дорогого и неэластичного материала для производства игрушек.
И здесь начинается самое интересное. Чертёж. Это и есть главное в производстве. Чтобы сделать чертёж, надо придумать идею. Над этим работают несколько профессиональных художников-конструкторов, которые должны не только уметь рисовать и делать чертежи, но и быть настоящими технологами.
Это очень непростая работа. Сначала делается чертёж-черновик. Он проходит предварительное испытание на оборудовании. Исправляются недочёты, дорабатываются узлы в модели. И так до тех пор, пока модель не начнёт нам нравиться. А понравится она нам только в одном случае — если полностью будет соответствовать первоначальной идее по форме, качеству и содержанию. Сложность чертежа может быть разной — от магнитика на холодильник до модели конструктора поезда «Сапсан», модели танка, ажурной конфетницы или чайного домика-дворца.
Наша компания занимается лазерной резкой дерева относительно недавно, однако менее чем за два года мы разработали около тысячи чертежей. Каждый день выходит от трёх до десяти новинок. В четыре раза мы увеличили парк оборудования. Это говорит о том, что спрос на нашу продукцию большой. Она нравится покупателям.
Как молодая, но уже зарекомендовавшая себя на рынке компания, мы ставим себе почти нереальные цели. Ломая стереотипы, мы сказали себе: дерево — это прекрасно. Оно должно быть доступно по цене и безупречно по качеству. Но если с качеством мы добились отличных результатов, то оставался нерешённым вопрос, как сделать дерево недорогим? Тут в дело вступает другая команда специалистов — маркетологи и экономисты.
Лазерный станок при всех своих достоинствах имеет существенный недостаток — он режет неторопливо. Есть определённое соотношение скорости и мощности, чтобы материал был прорезан насквозь. Следовательно, основная затрата — зарплата оператора. Это существенно увеличивает себестоимость продукции. Вот именно эту составляющую нам удалось оптимизировать. Мы выстроили технологическую цепочку таким образом, что затраты на оператора снижены в три раза без снижения уровня его оплаты.
Второй этап снижения затрат — уменьшение общепроизводственных расходов за счёт объёмов производства. Предприятие работает круглосуточно семь дней в неделю. Иными словами, мы просто не выключаемся. Это также влияет на себестоимость изделия.
Всё это позволило снизить издержки таким образом, что мы смогли предложить рынку цены, которые его приятно порадовали. Однако вернёмся к лазерному станку.
Чертёж готов, кнопка «Пуск» нажата, и вот начинается превращение листа фанеры в полуфабрикаты детали, из которых затем получатся шкатулки, серьги и браслеты, танки, паровозы, магниты, конфетницы, подносы, коробочки, конструкторы, основы для часов и многое-многое другое. Лазерный луч, как большой выжигательный робот, с точностью 0,1 мм послушно исполняет чертёж. С такой точностью резки полуфабрикаты собираются в конструкции с идеальным качеством. Но полуфабрикаты — ещё не изделие.
Далее наступает этап сборки. В дело вступает второй цех — сборочное производство. Без ручного труда здесь не обойтись. Каждая деталь в руках опытных сборщиков превращается в изделие, которое будет радовать людей. Это кропотливая и ответственная работа.
И вот изделие готово, осталось его упаковать и положить в коробку. Его ждёт путешествие от нашего склада до магазина, к нашим покупателям.
Наша работа хороша тем, что она приносит огромное удовольствие. Наш творческий поход передаётся поклонникам нашей продукции и рождает у них новые творческие идеи. От идеи до идеи — так рождается настоящая деревянная симфония!
Михаил Кесельман, генеральный директор
ООО Производственная компания «Полноцвет»,
г. Чехов, Московская область
- Комментарии